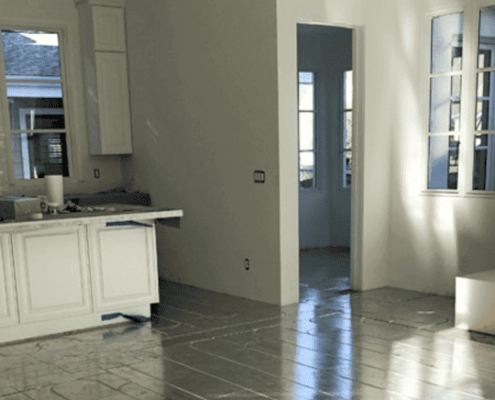
What Is Water Underfloor Heating? Everything You Need to Know
Water underfloor heating, also known as hydronic radiant…
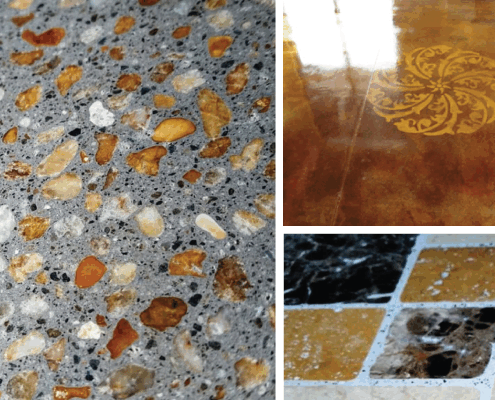
Great Ideas for Making Elegant Designer Cement Slabs
Beautiful Designer Cement and hot water radiant floor heating…
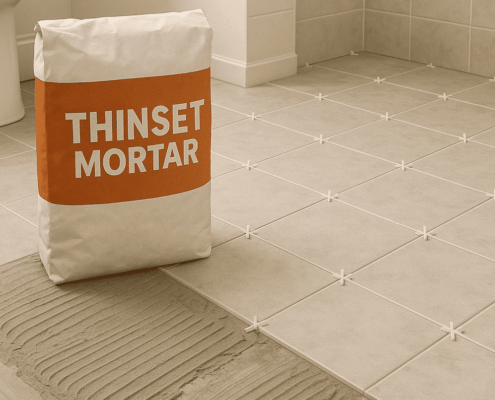
Modified vs. Unmodified Thinset: What to Use Over Radiant Floor Heating Systems
When installing tile over a radiant floor heating system,…
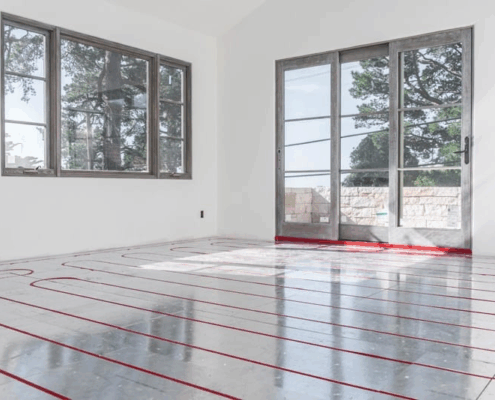
Underfloor Heating Repair: Troubleshooting and Fixing Radiant Floor Issues
Radiant underfloor heating systems offer some of the most…
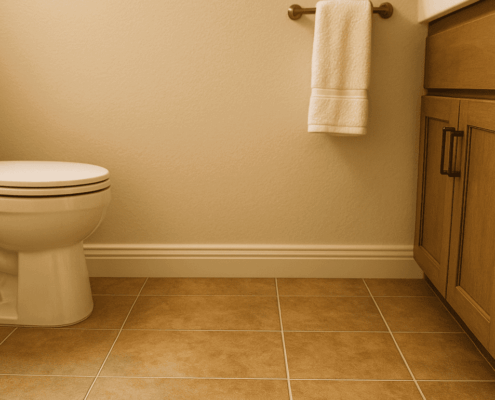
Electric Radiant Floor Heating: A Good Choice for Small Spaces
Radiant floor heating has become one of the most desirable…
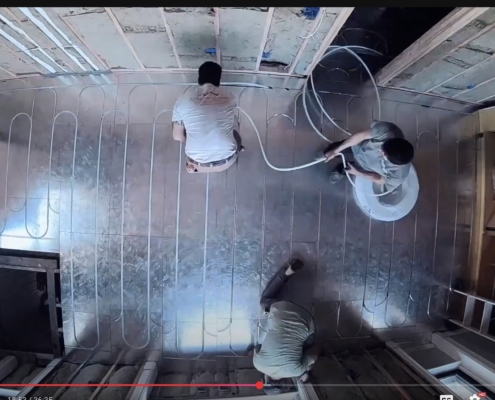
The Many Radiant Panels Offered By Warm Brothers Inc.
ABOUT THE MANY RADIANT PANELS OFFERED BY WARM BROTHERS…